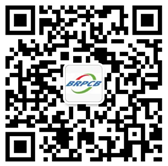
在航天、5G通信等高可靠性领域,陶瓷封装产品需承受-55℃~125℃极端温度、96小时盐雾腐蚀及长期机械应力。传统单层镀镍易因内应力集中导致镀层鼓泡剥落,且针孔贯穿会加速基体腐蚀。多层镍的镀覆技术,是指在同一基体材料上,选用不同的镀液成分及工艺条件,获得两层或三层的镍镀层,但是镀层总厚度却不增加甚至降低,而镀层的耐蚀能力却得到提高。那么,该技术有什么优势呢?
应力梯度设计,巧妙化解内应力
利用磷元素对晶体结构的调控,通过交替沉积不同磷含量的镍层(高磷镍磷含量10-12%,中磷镍7-9%),高磷镍层(磷含量10-12%)呈压应力,中磷镍层(7-9%)呈拉应力,通过“反向弹簧”式设计实现应力自抵消,避免镀层开裂。而且,高磷镍层在热处理中发生非晶态扩散,与柱状结构的半光亮镍形成应力缓冲带,有效抵消层间应力。该技术关键点主要在于:镀层顺序与厚度控制。工艺上,应严格遵循“基体→冲击镍(氯化镍体系)→高磷镍→小电流镍→中磷镍→镀金”顺序。其中镍层总厚≤11.4μm,镍层过厚会导致过多的应力累积。此外,还可通过热处理来释放镀层内部的内应力,进一步增加稳定性。譬如,470-500℃真空退火(≤5×10⁻³Pa)消除氢脆,同时促进高磷镍层扩散,增强层间冶金结合。
针孔错位设置,有效阻断腐蚀通道
各层镍的针孔分布随机且独立,多层叠加后针孔贯穿概率大幅降低。实验表明,四层结构可将盐雾耐受时间从24小时提升至96小时以上。
镍层盐雾腐蚀的SEM图片
此外,最外层的金层(厚度0.1μm及以上)主要提供惰性防锈屏障,内层的镍层作为牺牲阳极。当腐蚀介质渗入时,高硫镍层(含硫0.1–0.25%)优先横向腐蚀,保护基体。该关键点在于电流密度精准调控。小电流电镀镍(0.1–2A/dm²)填充底层微孔,硫酸镍浓度降至160–180g/L,避免高电流导致针孔扩大。镀液纯净度保障:采用超声波碱性除油+盐酸活化(pH 0–4)彻底清除陶瓷表面氧化物,从源头减少针孔生成。