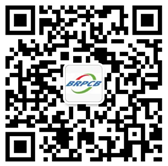
IPC-A-610 标准已对分层起泡给出明确的定义。起泡:一种表现为层压基材的任何层与层之间,或基材与导电薄膜或保护性图层之间的局部膨胀与分离的分层形式;分层:印制板内基材的层间,基材与导电箔间或其它间的分离。
1、铜箔与粘结片树脂之间分层
铜箔毛面的表面粗糙度大,或者瘤化程度高,铜箔与树脂接触的比表面积就大,那么铜箔和树脂的结合力(抗剥离强度)就大,出现铜皮分层的情形将大大减少。
爆板位置进行切片观察,发现芯板的铜箔和树脂之间发生分离,见下图。这种界面分离原因从两方面考虑:第一,焊接时基材受热膨胀过大;第二,两者界面本身的结合力弱,而造成两者结合力弱的原因比较复杂。
2、粘结片树脂之间分层
多层PCB的压合过程分为预压和全压两步。预压在较低的接触压力下(大多数板材的预压压力为0.69-1.37MPa),使粘结片处于熔融温度(60~140℃)时完成层压排气、树脂填充层间空隙和初期黏合等。全压在较高的接触压力(1.96-3.92MPa)和粘结片交联温度(160-170℃)条件下,完成树脂由熔融到交联固化的转化。
预压周期太短,即过早地施加全压,会造成树脂流失过多,严重时会造成缺胶分层;而预压周期太长,即加全压太晚,层间空气和挥发物排除得不彻底,间隙未被树脂充满,便会在板内产生树脂空洞,在后工序再次经高温冲击时,可能会由于气体膨胀而分层。
经过高温压合,粘结片的树脂分子聚合成链,将两张粘结片紧密结合在一起。而它们之间存在的杂物,会阻碍树脂之间的聚合,削弱粘结片之间的结合力,在受热膨胀时出现分层。
3、粘结片树脂与棕化面之间分层
内层芯板经过棕化处理后,在铜面形成一层均匀的棕色有机金属膜,可增强铜面与粘结片的结合力。同时,在高温压合过程中,阻止铜与粘结片的氨基发生反应。棕化面通常呈现出均匀棕色和形凸起状的微观形貌能够增大内层铜面与粘结片树脂间的物理结合力,在压合过程中还能与树脂分子发生交联反应形成化学键合,增强树脂与铜面的结合力。当棕化面的这种微观结构被破坏,如刮伤,或者棕化异常时,会削弱棕化面粘结片树脂的结合力,导致受热膨胀后易出现分层现象。
粘结片由玻纤和树脂组成,树脂在高温下具有流动性,冷却后与铜面结合。当铜层过厚时,压合会使大量树脂向无铜区流动,导致与铜面结合的树脂层偏薄。此外,棕化面的污染也会削弱粘结片树脂与棕化面的结合力,导致分层。
4、玻纤与树脂之间分层
玻纤与树脂之间的结合力主要受材料固化体系和水分子作用的影响。目前常见的固化体系主要为双氰胺(DICY)固化体系和酚醛树脂(PN)固化体系。DICY体系树脂固化后,其高分子链含有较多的极性N原子,易与水分子形成化学键,发生水解,削弱树脂间的结合力,导致树脂与玻纤发生分离。研究表明,DICY固化体系在残铜率为80%时,吸水率达到0.41%(质量分数)后回流一次(无铅回流工艺,峰值温度约245℃)就会出现玻纤与树脂之间分层。
此外,当PCB暴露于缺乏有效监控的环境中或时间存储时,环境中的水分会慢慢向板材内部渗透。在回流焊的高温下,当水分蒸发形成的蒸汽压力大于板件内部的结合力时,就会出现分层爆板。蒸汽压力主要受回流温度和吸水程度的影响,含水越多,回流峰值温度越高,蒸汽压力越大。同时,大铜箔面会挡住了受热后向外逸出的水汽,使微裂纹水汽的压力升高,导致爆板概率进一步增大。
5.芯板铜箔与树脂之间分层
芯板铜箔与树脂之间的结合力,与外层铜箔和粘结片树脂之间的结合力一致,主要为物理结合力。因此,发生分层的原因类似,也包括铜箔毛面的表面粗糙度小或者瘤化程度低、板材异常和钻孔质量差等。