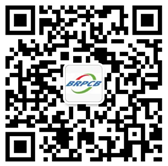
氧化铝陶瓷基板作为雷达微波组件的核心部件,不仅是半导体芯片、电子元器件封装的机械支撑载体,而且还提供内部电路的互连以及电路散热的通道。微波组件高频段、高集成和高散热的发展需求,对陶瓷基板集成器件的密度、性能等的要求不断提 高,对陶瓷基板微孔及微群孔的加工质量和效率的要求越来越苛刻。然而,氧化铝陶瓷基板属于高硬脆材料,采用传统加工方法加工极易使其产生裂纹,甚至断裂,加工废品率较高,制约了雷达微波组件的制造。
激光加工作为一种非接触式加工方式,极其适用于传统加工工艺无法加工的高硬度、高脆性及高熔点材料。其加工精度和加工效率高,加工柔性好,极易与计算机、信息、机器人等技术融合,非常适合高密度群孔加工。雷达微波组件中氧化铝陶瓷基板常用的孔结构特征尺寸一般为100500m,在激光加工中常采用光束沿一定轨迹旋切的方式进行材料去除,以达到精准调控孔特征尺寸的目的。然而,目前国内对氧化铝等陶瓷材料激光打孔的研究主要集中在冲击法打孔与激光烧蚀机理方面,对旋切法加工中精准调控特定尺寸孔结构的工艺研究较少。
1、氧化铝陶瓷
氧化铝陶瓷是指以三氧化二铝(Al2O3)为主要原料(含量在75%以上)、以α-Al2O3为主晶相的陶瓷。氧化铝陶瓷的机械强度和硬度高,绝缘性能、耐热冲击性能和抗化学侵蚀性能良好,与金属的附着力好,是一种综合性能较好的陶瓷基片材料。实验材料为电子封装基板常用的Al2O3含量为96%的0.12mm厚的氧化铝陶瓷,其基本性能参数为:密度3.6g/ cm3,硬度1500,抗弯强度3000kg/cm2,抗压强度25 000kg/cm2,导热系数25W/(m·K),介电常数9.4,热膨胀系数6×1067×106 C1。实验所用实物样片及纳秒激光加工系统如图1所示。
2、纳秒激光加工系统
实验采用的激光器为FOTIA-355,输出激光波长355nm、脉冲宽度11ns 的紫外纳秒激光。激光器出口光束直径为1.1 mm,标称光束椭圆度为97.1%,光束质量因子为 1.12,光束发散角为1.2mRad。纳秒激光实验平台及主要参数如图1(b) 所示。纳秒激 光加工实验台的光路系统由一个扩束镜、一个小孔光阑、一组反射镜、一个二维振镜和一个场镜组成。 扩束镜扩大倍数为10倍,经过扩束镜后,激光器的出口光束直径增大到11mm。小孔光阑设定孔径为7.5 mm。激光光束经过反射镜传导进入二维振镜系统。实验振镜型号为61710PS1XY2-TH,入射波长为355nm,孔镜尺寸为10 mm,扫描角度为±22,扫描范围为70 mm×70mm。场镜型号为TSL-355-50-103Q,设计波长为355 nm,焦距为103mm,扫描范围为50mm×50mm。激光经光路系统最终到达样品表面的实际加工聚集光斑直径为10m。
3、纳秒激光旋切轨迹设计
实验目标为在氧化铝陶瓷基板表面加工常用的孔入口直径为200m的通孔,拟采用同心圆填充激光孔加工,如图2所示。首先,通过软件画一个直径为R的外圈圆形(本实验中R值为180m)。然后,采用同心圆对外圈圆进行填充(本实验中设置的同心圆 间距H为15m)。设定激光由内向外进行同心圆扫描加工,激光扫描速度为 v,完成一次由内向外的同心圆加工等同于完成1次扫描,可以设定多次扫描。
4、激光平均功率对孔特征尺寸的影响
如图3中实线所示为纳秒激光加工氧化铝陶瓷表面孔入口直径与激光平均功率的关系。从图中可以看出,孔入口直径随激光平均功率的增大而增加。其主要原因是激光能量增大使得氧化铝陶瓷加工区域吸收的热量增多,烧蚀区域体积扩大,导致更多的材料气化或液相喷溅去除,增大了孔入口直径。孔出口直径也随着激光平均功率的增大而增加,如图3中虚线所示。然而,与孔入口直径相比,孔出口直径的增幅明显减小。以扫描速度为100mm/s的直径变化曲线为例,激光平均功率从5W 增大到8W 时,孔入口直径增大了20 m,而孔出口直径仅增大了8m。这主要是因为在纳秒激光加工氧化铝陶瓷的过程中,已成型的孔通道和通道内的等离子体会反射部分激光量,导致实际作用于孔出口位置的能量减弱,材料去除相对较少。当激光能量增大时,这种衰减作用更加明显,孔出口处吸收的能量增量显著小于孔入口处吸收的能量增量,因此孔出口直径增加量比入口直径增加量小。
如图4所示,孔的锥度随着激光平均功率的增大而增大,即随着激光平均功率的增加,孔入口直径的增幅比孔出口直径的增幅更明显。其中一个原因是在激光能量作用下,熔池在热传导下产生的径向扩张比深度方向的扩张更加明显。然而在采用毫秒激光冲击法加工氧化铝陶瓷时,孔锥度出现了相反的变化规律,即孔锥度随着激光能量的增大而减小,甚至出现负锥度。这是由于毫秒激光的长脉宽特性使得加工区域积累大量热量形成熔池,当激光能量增大时,熔池上方的高压蒸汽产生反冲压力作用于熔池熔体上,推动熔融材料沿着孔通道向上排出,并在重力用下喷溅到孔顶部周围,重新凝固形成重铸层。孔入口被重铸层覆盖,导致其直径减小,而孔出口在熔融物排出侵蚀过程中持续扩大,最终导致孔锥度减小。对电子陶瓷基板的导通孔而言,短脉宽和超快激光器可以加工出无重铸层和具有适宜正锥度的孔,更有利于后续镀金属工艺。然而,超快激光虽然可以加工出无重铸层的孔,但其加工效率较低,成本高昂,显然不适用于陶瓷基板导通孔加工的工业化应用。因此,紫外纳秒激光无疑是更理想的选择。
5、激光扫描速度对孔特征尺寸的影响
扫描速度指在加工过程中激光光斑在加工样品表 面的运动速度。它控制着加工路径上激光的脉冲重叠个数,影响样品表面加工区域单位面积内吸收的能量大小。扫描速度越快,加工区域单位面积内接收的脉冲数就越少,吸收的能量就越少。为了深入研究纳秒激光氧化铝陶瓷表面孔加工过程中扫描速度对孔入/出口尺寸的影响规律,设置激光平均功率为8W,扫描次数为5 100次,扫描速度为20100 mm/s,实验结果如图5所示。从图5可以看出,随着扫描速度的增大,孔的入口和出口直径均逐渐缩小。这主要是因为增大扫描速度会减小氧化铝陶瓷表面加工区域单位面积内吸收的能量,降低激光能量对材料的去除作用,导致孔入/出口直径减小。
如图6所示纳秒激光加工氧化铝陶瓷表面孔锥度与扫描速度的关系,其中,当扫描次数为5次时,孔锥度随着扫描速度的加快而增大。这主要是由于5次的扫描次数不足以完全烧蚀出成型通孔,在加工出初始孔入口形貌、孔入口直径基本固定时,孔通道内及孔出口处的材料还没有完全去除。此时降低扫描速度,增大加工区域单位面积的脉冲重叠率,将会在孔通道内积累更多激光能量用于材料去除,孔出口直径增幅远远大于孔入口直径增幅,孔锥度减小。当扫描次数为10次时,这种烧蚀不完全的情况只发生在扫描速度大于80mm/s的范围内,所以当扫描速度从100mm/s降低到80mm/s 时,孔锥度从10.6降低到8.4。在扫描次数为10次、扫描速度低于80mm/s 时,孔基本成型,孔入/出口直径已接近于饱和,此时孔锥度基本保持不变。当扫描次数为 35次和100次时,扫描速度20100 mm/s 范围内的孔已完全成型,孔锥度基本不受扫描速度的影响。
6、激光扫描次数对孔特征尺寸的影响
扫描次数即为孔图案加工的循环次数,决定氧化铝陶瓷表面孔加工区域接收的总脉冲数和吸收的热量。较多的扫描次数可以对氧化铝陶瓷加工区域起到更充分的烧蚀和材料去除,形成形貌完整的通孔,且在一定程度上降低孔锥度。为了研究在纳秒激光打孔氧化铝陶瓷过程中,扫描次数对孔尺寸的影响规律,设置激光功率为8W,扫描速度为20100mm/s,扫描次数为5100次。图7中实线所示为孔入口直径与不同扫描次数之间的关系曲线。从图中可以看出,在扫描次数为515 次时,孔入口直径随着扫描次数的增加而增大,当扫描次数多于15次时,孔入口直径基本保持不变。这主要是因为当扫描次数少于15次时,孔入口未完全成型,较多的扫描次数可以提高材料去除量,而在激光加工循环15次之后,受同心圆孔加工轨迹的限制,孔入口直径达到饱和。 出口直径随扫描次数的变化如图7中虚线所示。当扫描速度为20 mm/s 时,孔出口直径基本保持不变,为188 m。这表明在扫描次数为5次时,孔已完全烧蚀成型,出口直径已达到饱和,更多的扫描次数对已饱和的孔出口直径无影响。在扫描速度为60mm/s时,扫描次数从5次增加到20次,孔出口直径从164m增大到184m,在扫描20100次范围内,出口直径 185m保持不变,即孔出口直径在第20次时已达到饱和。当扫描速度为100mm/s 时,随着扫描次数从5次增加到50次,孔出口直径从161m增加到183m,在加工循环到第50次时孔出口直径达到饱和,饱和的出口孔径为183m。 换句话说,随着扫描速度的加快,饱和出口孔径略微减小。这是因为较快的扫描速度使得加工区域单位面积内接收的脉冲数减少,加工区域在一个加工循环中积累的热量较少,在下一个加工循环到来前,热量已部分散失,导致每个加工周期内已成型出口边缘温度始终保持在较低水平,无法带来更多的材料气化或熔融去除,最终导致饱和孔出口直径较小。用纳秒激光在AlN陶瓷上旋切孔时也发现了相似规律,即随着扫描次数的增加,孔入口直径保持不变,孔出口直径增大至饱和。对用冲击法加工陶瓷孔而言,扫描次数的概念与脉冲数类似,而实验中却发现孔的入/出口直径随着脉冲数的增加基本保持不变。这是因为用冲击法加工时,光斑直径恒定,作用于材料上的能量密度高于材料烧蚀阈值部分的尺寸恒定,最终导致孔的直径保持恒定。
如图8所示为纳秒激光加工氧化铝陶瓷表面孔锥度与扫描次数的关系曲线。从图中可以看出:孔锥度随着扫描次数的增加而减小,当扫描速度为100mm/s时,孔锥度在扫描进行到第50次时达到饱和,此时孔锥度为8.0;当扫描速度为60mm/s时,孔锥度在扫描进行到第10次时达到饱和,此时孔锥度为8.3;当扫描速度为20mm/s时,孔锥度不随扫描次数的增加而减小,这是因为较慢的扫描速度对孔出口材料去除起着促进作用,在较少的扫描次数下即能得到较大的孔出口直径,进而得到较小的孔锥度。
本文研究了紫外纳秒激光对0.12mm厚氧化铝陶瓷表面进行孔加工中激光加工参数(包括激光平均功率、扫描速度和扫描次数)对孔特征尺寸(包括入口直径、出口直径和锥度)的影响。
实验结果表明:增大激光平均功率可以有效提高孔入/出口直径和孔锥度;激光扫描速度通过控制加工区域单位面积上接收的脉冲数来影响打孔部位热量的积累,较低的扫描速度可以增大孔入/出口直径;激光扫描次数的增加可以明显增大孔入/出口直径。 除了孔的特征尺寸,孔的形貌特征,如孔入/出口表面的喷溅物、孔侧壁的重铸层、孔口及侧壁的裂纹等,也是评价孔加工质量的主要因素。后续将在尺寸优化的基础上,进一步探索激光加工参数对孔形貌质量的影响规律,进而获得单孔加工尺寸和形貌均较好的激光加工参数。为了试验氧化铝陶瓷基板的功能,需要在其表面进行大面积群孔加工。后续将在单孔最优加工工艺参数的基础上探索大面积群孔加工的最优路径规划等。