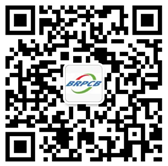
随着电子产品技术的发展和多功能化需求,为提高产品性能、产品组装密度、减少产品体积和重量,PCB的设计也日新月异。同时为了加大散热面积和加强表面元件器的安全性,满足通讯产品高速、高信息量的需求,需设计凹陷阶梯区固定元器件,阶梯盲槽设计应运而生。
同时随着电子、通讯产业的飞速发展,高频、RF设计越来越广泛,PCB上越来越多的运用到高频材料来满足信号传输的要求。为了满足客户对信号完整性以及信号接收与屏蔽匹配性等要求,在PCB设计上经常涉及高频盲槽,来满足信号传输速度和灵敏度。目前业界对于阶梯槽的制作,通常采用Low-flowPP压合+控深铣开盖工艺或内层开槽填充硅胶等缓冲材料工艺生产。然而采用常规工艺制作高频盲槽却存在许多问题,如偏位、流胶、板损等。
本文就采用常规工艺制作高频阶梯盲槽过程中出现的问题为切入点,主要介绍激光工艺制作阶梯槽,对高频阶梯盲槽的设计可实现性进行研究。
常规制作阶梯槽工艺
目前阶梯槽制作工艺,常规采用Low-flow PP低流动半固化片压合+控深铣开盖工艺或内层填充硅胶等缓冲材料的工艺生产。以下仅列出阶梯槽工艺相关流程:
根据以上工艺流程特点,可以看出,此种阶梯板制作工艺重点管控制成较多,操作流程复杂。采用上述工艺制作高频阶梯槽,存在以下问题点:
偏位
阶梯槽制作,芯板先开槽后压合,制作过程中存在偏位风险。对其影响流程有内层芯板预防,芯板开槽、PP开槽、层压压合等。如图2所示,当层压后,阶梯槽出现偏位,阶梯槽大小变形,客户无法固定元器件,影响装载性能。
流胶
常规制作,PP开窗比槽大0.5mm。高频阶梯槽制作中PP开窗大0.5mm,流胶严重,如图3所示,槽底溢满流胶。高频阶梯槽PP开窗比槽大1.0mm,如图4所示,流胶量减少,但可以看出,开窗区域明显发生凹陷,槽边的芯板与芯板间已无介质层,相互接触导通,影响品质。由此,可知,相应继续开大窗,胶也会被挤出流入槽内,并且可能出现缺胶、变形等品质缺陷。
板材破损
随着PCB板小型化发展,板材厚度、阶梯槽深度也趋向小型化,板材也越变越薄,槽也越变越浅。采用常规工艺制作阶梯槽,层压后开窗区板面易产生凹陷(如图6),影响后续流程控制,甚至开窗区破裂。常规采用PE+离型膜方式复型,但效果不明显。
本文针对常规制作工艺问题点,对高频阶梯槽的设计进行优化,采用激光工艺制作阶梯槽,实现对高频阶梯槽的设计。
激光制作高频阶梯盲槽工艺
难点分析
常规工艺制作高频阶梯槽主要出现偏位、流胶、板损问题。
板损
主要由于层压开窗,存在高度差,导致板材受损,常规使用复型材料复型,但开窗面积大,加上芯板越来越来薄,效果不是很明显。所以针对板损问题是否可以不开窗制作高频阶梯槽。通过调研,目前采用CO2激光制作HDI盲孔,对此可以采用CO2激光钻孔方式制作盲槽。但采用HDI参数制作盲孔很容易伤害槽底铜。对此,设计槽位置蚀刻成光板(如图7),采用除胶低能量钻槽,保证不伤害槽底铜面。
图7 芯板槽区域蚀刻图形
流胶
常规使用PP都是Low-flow,且开窗比槽大0.5mm,致使流胶问题得意解决。但使用高频材料制作阶梯槽时,PP含有一定胶,通过开窗无法解决流胶问题。对此只能后续采用激光除胶解决流胶问题。
偏位
由于经过前工序流程,常规制作工艺很容易层压后偏位,造成元器件固定不良。而采用激光制作,可以解决槽壁由于偏位造成的凹凸不平。
综上,高频阶梯槽制作,芯板不开窗直接压合,槽位置铜蚀刻成光板,采用激光钻孔制作。然而采用钻孔方式制作槽,对于槽内孔的排列方式、激光能量设定尤为重要。排列方式关系到孔的密集程度,孔越密,对应的位置能量越大,当能量超过PP承受能力时,很容易烧焦槽壁,致使后续品质问题。而激光能量直接影响到槽的深度,同时当激光能量过大,很可能击穿槽底铜面。所以槽内激光孔排列方式、激光能量是激光制作的两个难点,以下对两种因素进行探讨。
槽内激光孔排列方式验证
采用高频材料Ro4350B验证槽内排孔情况,制作4*2mm盲槽,常规激光孔4mil,槽设置4mil激光孔排列铺满(图8),两孔孔心最大2.7mil铺满无缝隙。在铺满情况下,设计不同孔密集度分别按3种:(260个、370个、1040个)/平方毫米,设计如下:
图8 槽内激光孔排布
通过上述验证,在相同条件下,孔数多到一定程度,烧蚀槽壁,如3中所示。所以激光孔密集度影响高频阶梯槽质量。建议后续孔密集度不能超过1040个/平方毫米。
激光能量验证
采用常规能量制作盲槽,当槽越来越深,激光能量越来越大。当激光能量大到一定程度时,很容易烧蚀槽壁(如图9),影响后续制作品质,所以对激光能量最大值进行验证。
设计槽深1.5mm的高频阶梯槽,加大激光能量制作,能量设计分别为:(8、10、12、14、16、18)mJ
当能量为18mJ时,槽壁很容易被烧蚀,如上图9所示。当槽壁被烧蚀,严重影响品质,后续难以化学沉铜,同时也不美观。综上,对于18mJ制作的槽时,改用小能量多次激光钻孔。
综上,对于槽内激光孔,采用4mil孔径,两孔孔心间距不能超过2.7mil,密集度不能超过1040个/平方毫米。当激光能量超过18mJ时,改用多次激光钻孔制作。
流程设计:
(1)芯板制作:对于盲槽区域,蚀刻掉铜,对后续激光钻孔可以采用除胶能量制作,减少伤害槽底铜面影响。
(2)压合:正常参数压合,不能复型材料,减小必要麻烦及成本
(3)外层线路:主要蚀刻外层槽区域铜皮,对后续激光钻孔可以采用除胶能量制作。对于金属化及非金属化槽,此流程需特别注意。金属化槽,则沉铜前需激光钻出盲槽,则此流程安排在沉铜前。对于非金属化槽,则沉铜后激光钻出盲槽,则此流程安排在沉铜后,也就是板镀后制作。
(4)激光钻槽:首板制作,确定激光能量。
文件设计主要为盲槽区域线路设计及盲槽激光孔排布。
盲槽区域线路设计
考虑采用HDI盲孔激光钻孔容易伤害底铜。所以建议采用小能量制作,刚好除去树脂及玻纤,而不损害铜面。所以对于槽区域铜皮蚀刻,漏出基材。内层盲槽区直接干膜蚀刻掉铜皮,外层盲槽区层压以后根据客户设计槽内金属化要求安排干膜蚀刻外层铜皮。
槽内激光孔排布设计
采用4mil孔,紧密排布,两孔孔心间距最大2.7mil,不能超过此间距,否则出现空隙。同时孔密集度不能超过1040个/平方毫米。
成品清洗
经过上述设计、优化采生产高频阶梯槽,可以避免偏位、流胶、板损带来的干扰。激光钻孔后,过等离子除胶+酸洗+喷砂,阶梯区铜面洁净有光泽,槽壁无烧蚀情况,整个阶梯槽平整,如图:
总结
本文通过常规盲槽板制作工艺分析,对常规工艺制作高频盲槽板出现的偏位、流胶、板损问题为切入点。通过设计、流程优化,得到高频阶梯槽,实现了高频阶梯槽的加工的可实现性。通过上述制作,得到以下结论:
采用上述激光工艺制作高频阶梯槽,可以解决常规工艺带来的流胶、板损等缺陷。
层压前芯板不开窗,对于层压可以采用常规参数制作,无需复型材料,减少成本制作。
使用激光钻孔制作,阶梯槽区域蚀刻掉铜皮,采用低能量参数制作,减小激光对槽底铜皮影响,能量不能超过18mJ,对于超过此能量高频阶梯盲槽,采用低能量多次激光钻孔制作。
槽内激光孔排布,采用4mil激光孔,孔心间距不能超过2.7mil,孔密集程度不能超过1040个/平方毫米。