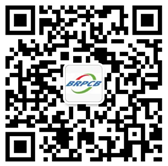
本文就应用于IC载板的CO2激光直接钻通孔工艺进行了深入的探讨,对制作开口孔径为70μm的通孔进行流程和参数优化。通过JMP软件设计优化试验,分析了各加工参数(脉宽、能量、枪数、光罩等)对开口孔径和孔真圆度的影响,并得出了最佳加工参数。最佳工艺参数为:脉宽7.1μs,能量6.9mj,光罩1.9mm,枪数2shot,同时微蚀量控制在0.6~0.8μm,以此加工所得开口孔径为70.96μm,真圆度为97.26%。在此基础上,对孔的可靠性能进行验证,验证结果证实了IC封装载板孔的可靠性能良好。
1.前言
随着集成电路线宽从57nm向28nm或更小尺寸转变[1],作为芯片载体的IC载板互联密度迅速增加。常规FC-CSP,MCP等产品导通孔数量高达500~600孔/cm2,孔径也由传统100-150μm缩小至70-80μm。传统的机械钻孔工艺无论在成本、产能还是精度等方面都已难以满足这类产品的量产要求。
激光通孔技术是特别针对高密度IC封装基板层间贯通孔加工的新型制造技术[2]。该技术利用基板介质层薄(一般0.04~0.15mm)的特点,结合激光快速成孔的优势,可有效应对FC-CSP等产品层间导通孔加工要求。但由于铜箔对CO2激光的吸收率低,目前普遍采用开窗或表面黑化/棕化作为激光钻孔前处理方式。其中蚀刻工艺流程长、成本高,且正反面曝光偏差易降低激光通孔的对准度;表面黑化或棕化可有效提高激光吸收度[3-4],但黑化或棕化工艺板面需要经过2-3μm微蚀,对于使用2/3μm薄铜基板的FC产品也不太合适。因此,开发一种适用于2/3μm薄铜基板的直接激光通孔技术十分必要。
本文就薄铜IC封装载板BT料CO2激光直接钻通孔工艺进行了深入的探讨,通过微蚀量测试优化了工艺流程,降低了溅射铜对线路制作的影响;通过JMP软件设计优化试验,分析了各加工参数(脉宽、能量、枪数、光罩等)对激光孔尺寸及真圆度的影响,得出了最优加工参数;在此基础上,通过高低温冲击及浸锡测试,分析了通孔结构的可靠性。
2.试验部分
2.1 试验材料及仪器
实验材料:IC封装基板专用覆铜板BT料,介质层厚0.1mm,表面铜厚2μm;
实验仪器:CO2镭射钻孔机、水平除胶沉铜线、水平连续电镀线、微蚀刻机、金相显微镜(NiKon)、高低温冲击箱(TSG-71H-W)、导通电阻测试系统(AMR-200-UD)、回流炉(ERSA Hot Flow 3/20XL)。
2.2 试验方法
2.2.1 试验流程
开料—钻定位孔—直接激光钻孔(TL面和BL面各加工1枪)—除Burr—除胶沉铜—电镀填孔—可靠性分析—切片分析
2.2.2 测试文件
激光钻孔文件设计为158×63的矩形阵列,孔连接方式采用菊花链方式设计,如图1所示。
2.2.3 流程优化
DLD加工时在孔周围不可避免的存在溅射铜(Burr),当Burr的尺寸超过激光孔AR(一般为20~25μm)时,可能影响干膜结合力并导致线路不良。普通PCB直接激光钻孔后通常通过磨刷去除孔口的溅射铜,但此方式很难应对0.1mm及以下厚度的产品。实验测试化学微蚀方式除Burr的流程,微蚀量变化与溅射铜关系如表1所示。
2.2.4 初始参数研究
对比测试能量E和光罩尺寸D的组合对孔径的影响,确定适合于2μm薄铜直接激光加工的能量密度d(单位为:mj/mm2) 。其中: d=4E/πD2 。
不同能量和光罩组合对应的能量密度如表2所示。
2.2.5 参数优化
使用JMP统计分析软件,通过响应曲面设计,对激光加工参数进行优化。以孔径和真圆度作为响应指标,以2.2.4分析结果及对应的脉冲宽度为基本参数,通过Screen DOE优选出最佳加工条件。因素水平设定如表3所示。
2.2.6 可靠性测试
根据2.2.3及2.2.5流程及参数优化结果,试制5个样品并依次进行预处理、高低温冲击和浸锡实验,实时监控高低温循环过程中样品电阻变化情况,并通过切片观察分析可靠性测试后的通孔结构形貌。可靠性测试条件如表4所示。
3.结果与分析
3.1 微蚀量对溅射铜的影响
溅射铜随微蚀量变化关系及微蚀后铜面形貌金相显微镜观察结果如图2-3所示。由图2可以看出,随着微蚀量增加,孔口溅射铜逐渐减少。控制微蚀量0.6μm以上,溅射铜尺寸将小于20μm,且大部分集中在孔口周围(如图3B所示),当微蚀量增加至1.2μm时,孔口溅射铜基本消失(如图3C所示)。
从图2-3可以看出,通过化学微蚀可以有效去除孔口Burr。但微蚀量不宜过大,否则容易导致孔口或板边漏基材,影响孔结构可靠性。为防止过度微蚀对线路图形的影响,在满足规格(Burr小于20μm)的前提下,控制微蚀量范围为0.6-0.8μm。
3.2 孔径与能量及Mask尺寸关系
激光孔尺寸与能量密度关系如图4所示。从图4可以看出,激光加工薄铜时存在一个能量密度阀值,当能量密度低于此阀值时(Stage-A),激光无法击穿铜箔成孔;激光越过此阀值后(Stage-B),随着能量密度增加,孔径急剧增大;随着能量密度进一步增加(stage-C),激光孔径增大,但增大幅减小,此时制约孔径大小的关键因素由能量密度变为激光光束尺寸。
此外,从图4中还可以看出,70μm孔径所需能量密度为1.50~2.00 mj/mm2,其对应的光罩尺寸范围为1.6~2.0mm,激光能量范围为6.0~8.0mj。
3.3 Screen DOE结果分析
3.3.1 Screen DOE试验结果
DOE参数优化试验结果如表5所示。从表中不难看出,该参数范围内所得开口孔径在61-79μm之间,覆盖了测试目标孔径70μm,且孔真圆度均在93%以上,满足目标90%要求。
3.3.2 模型可靠性分析
应用JMP软件自带的模型分析测试结果的可靠性,“预测值-实际值”图如图5所示。从图中可以看出,开口孔径的P值<0.05,实验值与真实值非常吻合[5]。这说明对于开口孔径,该实验参数范围设置合理,模型的结果可靠;对于孔真圆度,P值为0.0791,略大于0.05,有1个测试结果超出预测范围。
3.3.3 因子效应分析
应用JMP软件自带的模型分析各参数与响应的依赖关系,其结果如图6所示。
从图中可以看出,能量、光罩、脉宽对开口孔径的影响均显著,显著程度依次为能量>光罩>脉宽;开口孔径随能量和脉宽的增大而增大,随光罩的增大而减小。 开孔孔径主要和能量密度以及光斑直径相关,能量增大,能量密度增大,开口孔径增大;光罩增大,能量密度减小,开口孔径减小;脉宽增大,能量密度虽减小,但激光持续时间延长,热效应时间延长,开口孔径增大。
光罩和能量是影响真圆度的显著因素,脉宽对其影响小;能量越大,真圆度越低;光罩越大,真圆度越高。真圆度主要受成孔过程中热效应的剧烈程度的影响,热效应越剧烈,开口形状越不规则。能量增大,能量密度增大,热效应加剧,真圆度降低;光罩增大,能量密度减小,热效应减弱,真圆度提高。
3.3.4 模型预测及验证
通过JMP响应刻画器来预测最优加工条件,预测结果如图8:其中脉宽7.1μs;能量6.9mj;光罩1.9mm,预测的开口孔径为69.87μm;真圆度为97.75%。
对预测出的最优加工参数进行验证,开口孔径和真圆度实际值与预测结果基本一致,开口孔径实际测量值为70.96μm,真圆度实际测量值为97.26%,加工效果如图8。以上结果均在控制标准以内,且开口孔径CPK>1.67,满足制程要求。
3.4 可靠性测试结果
样品高低温冲击过程中电阻变化如图9,其中左图为高温电阻,右图为低温电阻。所有试片经高低温冲击测试后,阻值变化均未超过10%,测试结果为通过。
对试样进行切片分析,结果如图10,切片结果显示无孔铜断裂,孔壁分离现象,孔内品质良好,说明孔结构性能可靠。
4.结论
激光直接钻孔工艺用于IC载板基板贯通孔量产加工在成本、效率和孔位精度等方面优势明显,同时直接钻孔所带来的板面溅射铜残留和孔型不佳等风险可以通过对激光加工参数和流程加以优化得到改善。
脉宽、能量、光罩和枪数对激光孔型都有很大影响,本次试验在枪数固定为两枪(TL面和BL面各加工一枪)的情况下,以开口孔径和真圆度为指标设计优化试验,得到了脉宽、能量和光罩对响应的影响规律以及最佳加工值。最优加工参数为:脉宽7.1μs,能量6.9mj,光罩1.9mm,枪数2shot。各因素对开口孔径的影响大小为:能量>光罩>脉宽;对真圆度的影响大小为光罩>能量>脉宽。对于溅射铜的消除,采用化学微蚀的方式,将微蚀量控制在0.6~0.8μm范围内,可达到良好的去除效果。试验最后对加工后的试样进行回流焊、热应力和高低温冲击等可靠性测试,测试结果合格,证实了孔的可靠性能良好。
从以上结果来看,应用该加工参数和流程加工激光通孔可以满足产品品质要求,上述工艺可以导入生产。同时针对不同板材、不同芯板厚度以及不同目标孔径大小,均可采用上述试验思路和方法来进行激光直接钻孔测试